Understanding Precision Mold Components in Metal Fabrication
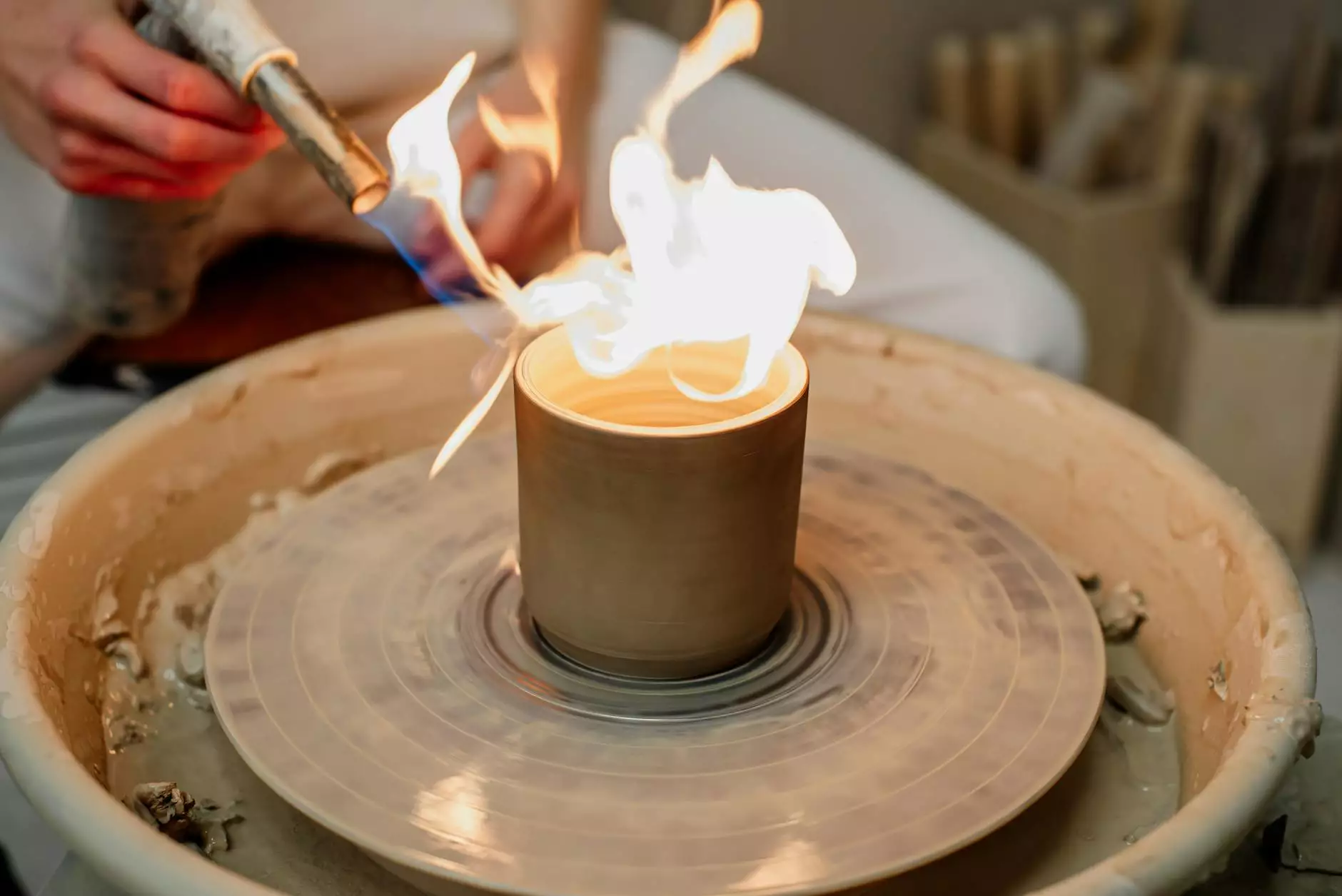
Precision mold components are critical in the realm of metal fabrication, serving as the backbone of numerous manufacturing processes. The manufacturing industry has grown tremendously, and with it, the need for high-quality, accurate, and reliable components. This article delves into the various aspects of precision mold components, their significance, benefits, and how they contribute to the overall efficiency of the metal fabrication industry.
The Role of Precision Mold Components
At the core of manufacturing processes, precision mold components are essential for producing consistent and high-quality products. These components are used in various applications, including:
- Injection Molding: Used to create complex shapes with high precision.
- Die Casting: Perfect for producing parts with intricate designs.
- Stamping: Ideal for creating metal parts in bulk with rapid production rates.
- Extrusion: Helps in forming materials by forcing them through a die.
Benefits of Using Precision Mold Components
Investing in precision mold components offers several advantages that can significantly enhance the manufacturing process. Here are some key benefits:
1. Enhanced Product Quality
Precision mold components are manufactured to tight tolerances, ensuring that each part meets the exact specifications required. This high level of accuracy translates to better product quality and performance. Companies utilizing these components experience fewer defects and higher customer satisfaction rates.
2. Increased Efficiency and Productivity
With precision components, the manufacturing process becomes more streamlined. This is due to:
- Reduced setup times, as components are designed for quick interchangeability.
- Fewer rework cycles as a result of higher accuracy in production.
- Improved cycle times as processes can run continuously without interruption for adjustments.
3. Cost-effectiveness in the Long Run
While the initial investment in high-quality precision mold components might be higher, the long-term savings are significant. Companies often witness:
- Lower scrap rates due to fewer defects.
- Reduced labor costs because of the efficiency of operations.
- Minimized downtime, leading to an increase in overall production.
Key Materials Used in Precision Mold Components
The choice of materials for precision mold components is crucial. Commonly used materials include:
- Tool Steels: Known for their hardness and wear resistance, tool steels are commonly utilized for manufacturing mold components.
- Aluminum Alloys: These are lightweight and offer excellent thermal conductivity, suitable for various molding applications.
- Polymers: High-performance polymers are often used in applications where corrosion resistance is essential.
- Copper Alloys: Effective for applications that require good electrical conductivity and thermal performance.
The Manufacturing Process of Precision Mold Components
The manufacturing of precision mold components involves several steps, each requiring specialized knowledge and technology.
1. Designing the Mold
The first step is to create a detailed design of the mold using CAD software. This design must take into account the functionality of the final product and the capabilities of the manufacturing process.
2. Material Selection
Choosing the right material is crucial. Factors such as production volume, complexity of the part, and surface finish requirements will influence this choice.
3. Machining and Fabrication
Advanced machining techniques, including CNC machining, are often utilized to achieve the necessary precision in fabricating mold components. This stage is pivotal, as any deviation can lead to significant issues in production.
4. Polishing and Finishing
Precision molds often require polishing and finishing processes to enhance surface quality and ensure that they can produce flawless parts. This step might include:
- Surface grinding
- Abrasive polishing
- Coating applications for added durability
Challenges in Manufacturing Precision Mold Components
Despite the numerous advantages, manufacturers may face challenges when producing precision mold components:
- High Initial Costs: The investment in precision machinery and skilled labor is often substantial.
- Complexity of Design Changes: Modifications to designs can incur extra costs and production delays.
- Maintaining Quality Control: Ensuring consistency and quality across large production runs can be challenging.
Future Trends in Precision Mold Components
The landscape for precision mold components is continuously evolving, with technology paving the way for advancements. Here are some trends to watch for:
1. Automation and AI Integration
The use of automated machinery and AI in the design and production stages is on the rise. These technologies enhance precision and speed up manufacturing processes.
2. Micro-Molding Techniques
As products become smaller and more intricate, micro-molding is gaining popularity. This technique allows for the creation of tiny, precise components that meet demanding performance standards.
3. Sustainable Practices
With a growing focus on sustainability, manufacturers are exploring methods to reduce material waste and energy consumption in the production of precision mold components.
Conclusion
In conclusion, precision mold components play a pivotal role in the metal fabrication industry, significantly impacting product quality, manufacturing efficiency, and cost-effectiveness. By understanding their importance, benefits, and the challenges associated with them, businesses can make informed decisions that enhance their operations. Embracing the latest trends and technological advancements will ensure that companies remain competitive in this ever-evolving landscape.
To explore more about precision mold components and how to integrate these processes into your manufacturing, visit DeepMould.net, a leader in the field of metal fabrication.