Understanding the Role of a Die Casting Tool Manufacturer
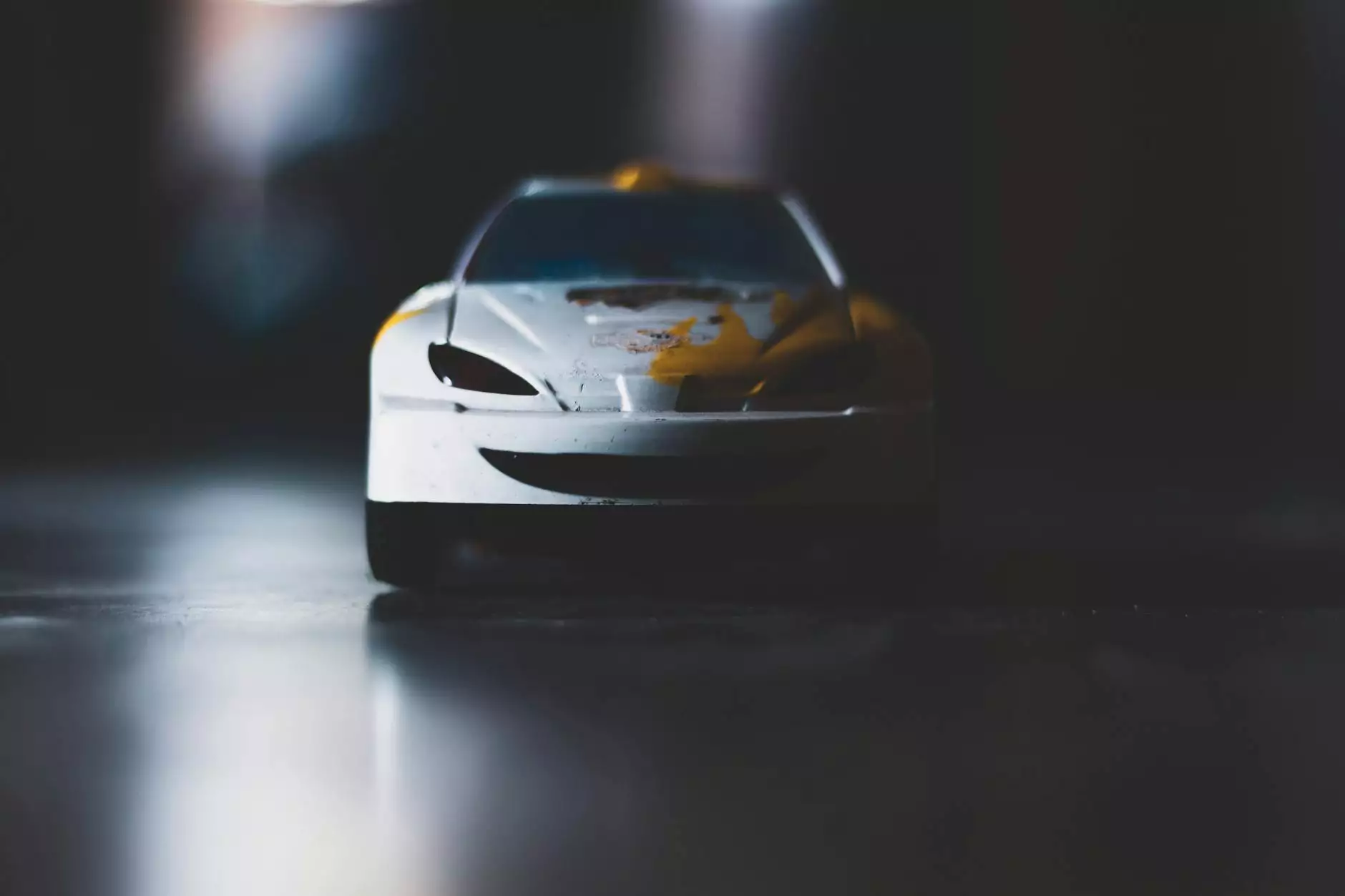
In today's fast-paced industrial landscape, the importance of die casting cannot be overstated. As a fundamental method in the metal fabrication industry, it enables manufacturers to produce complex shapes with exceptional precision and quality. At the forefront of this innovation is the die casting tool manufacturer, an organization that not only supplies the tools but also ensures that the whole process is efficient, reliable, and aligned with the ever-evolving industry standards.
What is Die Casting?
Die casting is a metal casting process that involves forcing molten metal into a mold cavity under high pressure. This process is ideal for producing parts with a high degree of accuracy and smooth surface finish. It's mainly utilized for non-ferrous metals, such as zinc, copper, aluminum, and magnesium. The intrinsic appeal of die casting lies in its ability to deliver high volumes of parts with minimal waste of material.
Importance of Die Casting in Metal Fabrication
This manufacturing process is critical in various industries:
- Automotive: Used for creating engine blocks, transmission cases, and other critical components.
- Consumer Electronics: Ideal for producing lightweight and complex enclosures for electronic gadgets.
- Aerospace: Enables the manufacturing of parts that require strict weight and strength standards.
- Medical Devices: Helps produce durable parts that meet stringent health regulations.
Advantages of Working with a Die Casting Tool Manufacturer
Partnering with a reputable die casting tool manufacturer like DeepMould provides numerous advantages:
- Expertise: Experienced manufacturers offer valuable insights into material selection and design optimization.
- Cost Efficiency: By minimizing material wastage and reducing production time, die casting can significantly cut down costs.
- Quality Assurance: Established manufacturers adhere to strict quality control processes ensuring that the final products meet industry standards.
- Customized Solutions: Tailored solutions specific to industry requirements guarantee that client needs are met precisely.
The Process of Die Casting Tool Manufacturing
The process of manufacturing die casting tools can be broken down into several critical steps:
1. Design and Engineering
The journey begins with precise design and engineering. Tooling designers work closely with clients to understand the specifications required for the finished products. This phase includes:
- CAD modeling to visualize the tool and product.
- Simulations to predict how molten metal will flow within the die.
- Prototyping to create a physical representation of the design.
2. Tool Fabrication
Once the design is finalized, the actual fabrication of the die begins. This involves:
- Machining the mold from high-grade steel or aluminum.
- Using advanced techniques like CNC machining for precision.
- Implementing surface treatments to enhance durability and performance.
3. Testing and Quality Control
Quality is paramount in die casting operations. Manufacturers must conduct various tests, including:
- Dimensional inspections to ensure conformity with specifications.
- Mechanical testing of the tooling for strength and longevity.
- Testing of the die casting process itself to validate the performance of the tooling.
4. Production Setup
After the tool passes inspection, it’s installed onto a die casting machine, ready for mass production. This stage includes:
- Tuning machine settings for optimal performance.
- Final checks to ensure everything is running smoothly before starting production.
Trends Shaping the Die Casting Industry
The die casting landscape is continuously evolving, driven by technological advancements and changing market demands. Here are some key trends to watch out for:
1. Automation and Robotics
The integration of automation and robotics in the die casting process is increasing productivity and safety. Automated systems can handle repetitive tasks, allowing human workers to focus on more complex operations.
2. Advanced Materials
With ongoing research, manufacturers are discovering new alloys and metal compositions that offer better performance in die casting. These materials can provide improved strength, lighter weight, and enhanced resistance to corrosion.
3. Environmental Sustainability
As industries become more environmentally conscious, die casting manufacturers are adopting more sustainable practices. This includes:
- Reducing energy consumption during the casting process.
- Enhancing recycling rates of scrap metals.
- Utilizing eco-friendly materials wherever feasible.
Choosing the Right Die Casting Tool Manufacturer
Selecting the appropriate die casting tool manufacturer plays a crucial role in ensuring the success of your projects. Here are some aspects to consider:
1. Industry Experience
Consider a manufacturer with extensive experience in your industry. Their familiarity with specific challenges and requirements will allow them to provide better solutions.
2. Quality Certifications
Ensure that the manufacturer adheres to international quality standards and holds relevant certifications, which reflect their commitment to excellence.
3. Customer Reviews and Testimonials
Research customer feedback. Positive testimonials can provide insights into the manufacturer's reliability, craftsmanship, and service quality.
Case Studies: Success Stories in Die Casting
To exemplify the effectiveness of engaging with a skilled die casting tool manufacturer, we can look into the success stories of companies leveraging die casting in their production processes:
1. Automotive Innovations
Leading automotive brands have collaborated with experts to develop complex components that meet the latest performance standards while staying lightweight. These partnerships have resulted in significant cost savings and efficiency improvements across vehicle production lines.
2. Enhanced Electronics Manufacturing
Consumer electronics brands have embraced die casting to produce high-quality enclosures that not only protect sensitive components but also enhance aesthetics. By working with proficient manufacturers, they have increased their production capacity without compromising quality.
The Future of Die Casting
The future is bright for the die casting industry, with advancements in technology paving the way for even greater efficiencies and capabilities. As a leader in the field, DeepMould is poised to remain at the forefront of innovation, continually adapting to meet the needs of our clients.
Conclusion: Why DeepMould Stands Out as a Die Casting Tool Manufacturer
Choosing DeepMould as your die casting tool manufacturer ensures that you have a partner committed to quality, innovation, and customer satisfaction. With decades of experience in the metal fabrication industry, we understand the nuances of the die casting process and deliver tools that empower your production capabilities.
Our commitment to precision, coupled with a customer-centric approach, makes us not just a supplier, but a true collaborator in your success. Whether you’re in the automotive, aerospace, or consumer electronics sector, DeepMould has the expertise and technology to help you excel in your field.
Contact us today to learn more about how we can assist you with your die casting needs.