Understanding Precision Injection Mold in Metal Fabrication
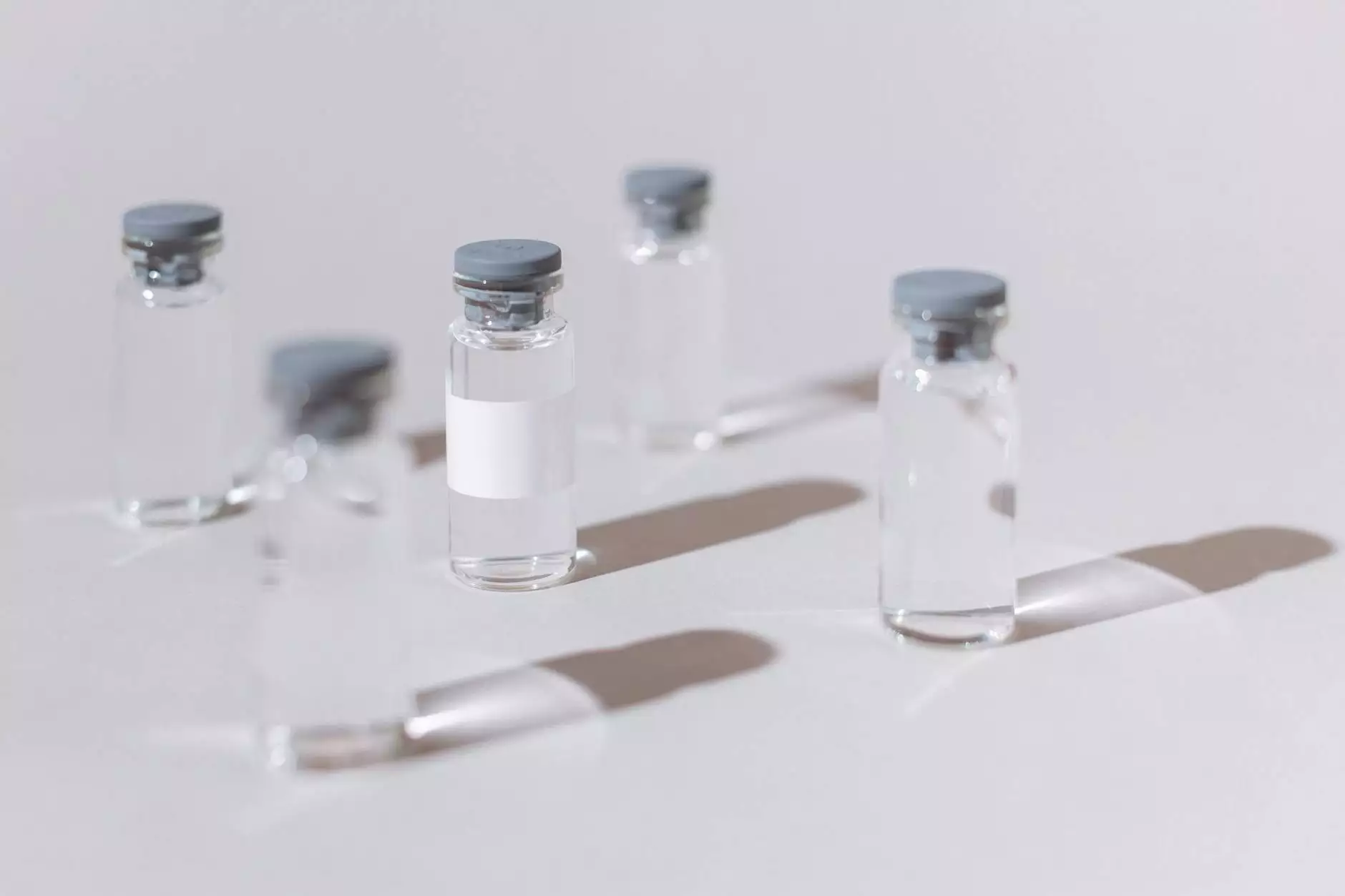
Precision injection mold technology has revolutionized the metal fabrication industry by enabling manufacturers to produce high-quality, complex parts with incredible efficiency. As businesses strive to optimize their production processes and reduce costs, understanding the subtleties of this technology becomes crucial for anyone involved in manufacturing or engineering.
What is Precision Injection Mold?
Precision injection molding is a manufacturing process that involves injecting molten material into a mold to create specific shapes and forms. This method is not limited to plastics but has extensive applications in metals and other materials, making it a versatile solution for many industries. The key to its success lies in the precision of the molds used, which allow for tight tolerances and detailed designs.
The Process of Precision Injection Molding
The precision injection molding process typically involves several critical steps:
- Material Selection: Depending on the application, manufacturers choose appropriate materials such as thermoplastics, metals, or alloys.
- Mold Design: Engineers create a mold design tailored to the product specifications, ensuring that the mold can produce components with the required precision.
- Injection: The selected material is heated until it becomes molten and is then injected into the mold at high pressure.
- Cooling: The injected material is allowed to cool and solidify, taking the shape of the mold.
- Demolding: Once cooled, the mold is opened, and the finished product is ejected.
- Finishing: Any necessary finishing processes, such as machining or surface treatment, are applied to meet specifications.
Benefits of Precision Injection Mold
Precision injection molding offers numerous benefits that make it an attractive option for manufacturers:
- High Efficiency: This method allows for rapid production rates, significantly reducing cycle times and increasing output.
- Consistency: The process produces highly uniform parts, which is critical for applications requiring tight tolerances.
- Cost-Effectiveness: Although initial mold production can be expensive, the cost per part decreases significantly with high volume runs.
- Design Flexibility: Precision injection molds can create complex shapes and intricate details that would be difficult or impossible to achieve with other methods.
- Material Versatility: This technology can handle a wide range of materials, from various plastics to elastomers and metals.
Industries Benefiting from Precision Injection Mold
The adoption of precision injection molding spans diverse industries:
- Automotive: High-quality component production is critical in automotive manufacturing, where durability and safety are vital.
- Electronics: Precision parts for electronics require tight tolerances to ensure functionality and reliability.
- Aerospace: The aerospace industry demands components that can withstand extreme conditions; precision molding meets these requirements.
- Medical: Medical device manufacturing relies on precision parts to ensure proper functionality and compliance with stringent regulations.
- Consumer Goods: The market for consumer products often requires innovative designs that precision molding can deliver.
Challenges in Precision Injection Molding
While precision injection molding has many advantages, it also poses unique challenges:
- High Initial Costs: The upfront investment in mold design and production can be significant.
- Complexity in Design: Designing molds for intricate parts requires expert knowledge and experience.
- Material Limitations: Not all materials are suitable for injection molding, and selecting the wrong material can lead to product failure.
- Maintenance Needs: Molds require regular maintenance to ensure they continue to produce high-quality parts.
The Future of Precision Injection Mold Technology
The future of precision injection molding technology looks promising, as advancements continue to emerge:
- Automation: Automated systems are enhancing efficiency and precision in the molding process.
- 3D Printing Integration: Integrating 3D printing with traditional molding methods improves prototype development and reduces lead times.
- Sustainable Practices: Industry leaders are exploring sustainable materials and processes to meet environmental standards.
- Smart Manufacturing: The implementation of Industry 4.0 technologies is allowing for real-time monitoring and process optimization.
Conclusion
In summary, the role of precision injection mold technology in metal fabrication is pivotal in today’s manufacturing landscape. From its efficiency and design flexibility to its wide-ranging applications, this method continues to be a game-changer in the industry. As advancements in technology pave the way for even greater precision and sustainability, businesses that invest in understanding and implementing precision injection molding will undoubtedly stay ahead of the curve.
Contact Us for More Information
If you are interested in exploring precision injection mold technology further or wish to discuss how it can benefit your manufacturing process, visit Deep Mould today. Our expert team is ready to assist you in leveraging this innovative technology for your business needs.